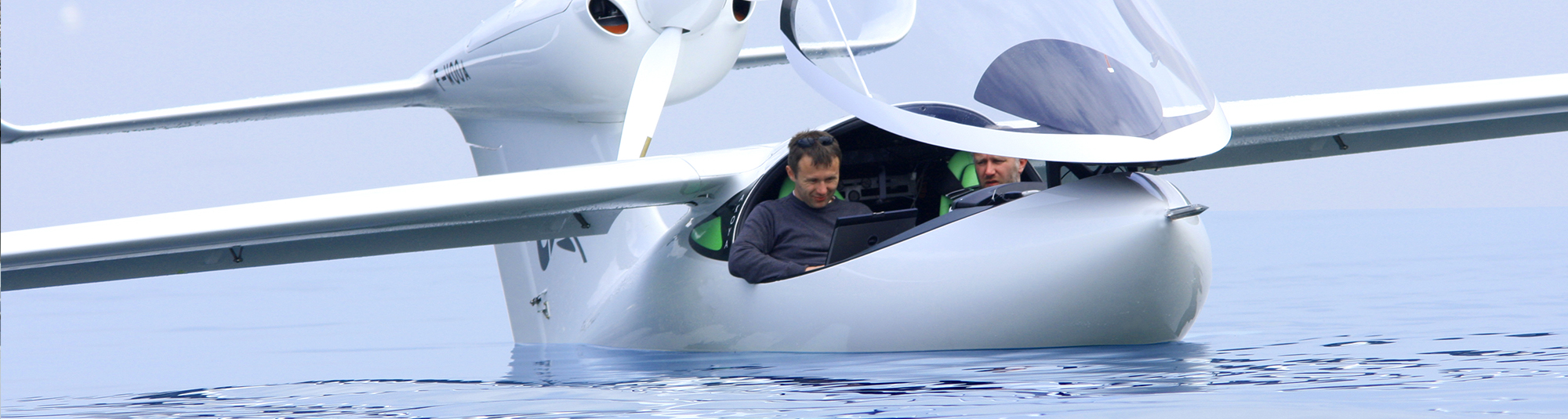
Creating a new generation of aircraft does, of course, not mean reinterpreting an existing aircraft design. We really had to design the aircraft from scratch, by putting all our assumptions aside, in order to see things from a fresh perspective and develop solutions that are radically different from existing ones.
A combination of brainpower, ingenuity, and rigor
Our R&D work is always based on our dreams and ambitious vision of aviation. Aerodynamics, hydrodynamics, engineering, materials science, and electrotechnology: armed with these skills, LISA’s highly skilled engineers demonstrate a high level of inventiveness, attention to detail, and rigor. The entire team enjoys meeting challenges in order to develop unique solutions in response to the “impossible challenges” that are an integral part of our approach.
Once the innovations are protected by international patents, our engineers can begin working on the aircraft with their rigorous scientific approach: analysis, structural testing, data recording and correlation, flight testing, and so on. All these stages are repeated until an manufacturable solution is achieved. And beyond the application of these solutions, our R&D engineers are responsible for building veritable know-how that can be used on other planes.
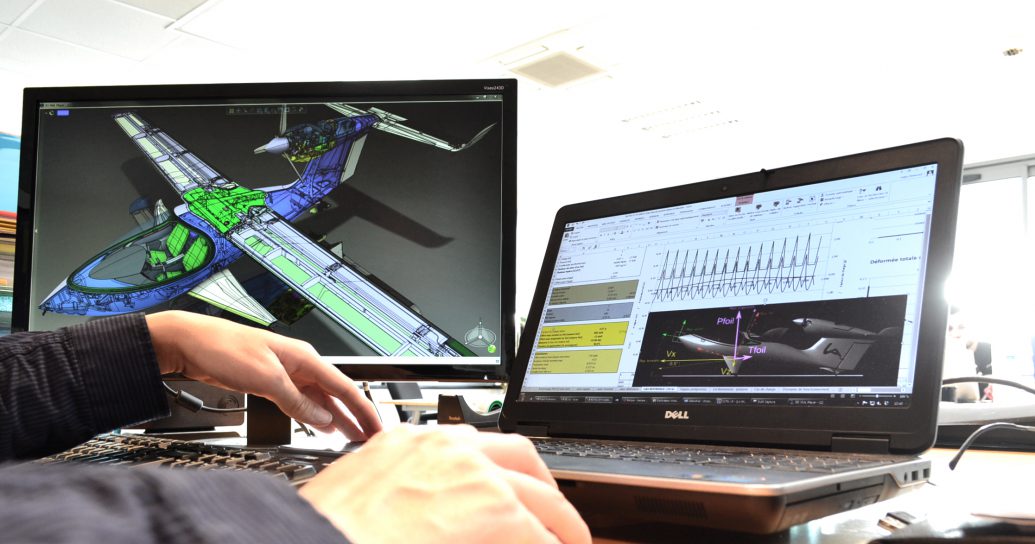
A well-established creative process
Translating the many inventive ideas from which our planes are comprised into concrete reality has required a great deal of work on the part of our engineers and years of research and development. Extensive studies combining the aerodynamic and nautical constraints were conducted to translate each of the concepts into material form, and then harmonize the ensemble, in order to achieve an optimal configuration.
When each configuration had been validated by calculations and digital simulation tests, it was subsequently tested on 1:3 scale models. Wind tunnel tests at the ONERA (the French center for aerospace research) made it possible to optimize the aerodynamic surfaces; the water-tank tests confirmed the properties of the “Seafoils,” and the tests on radio-controlled models in a natural environment made it possible to validate the principal flight characteristics and the aircraft’s maneuverability on each type of terrain.
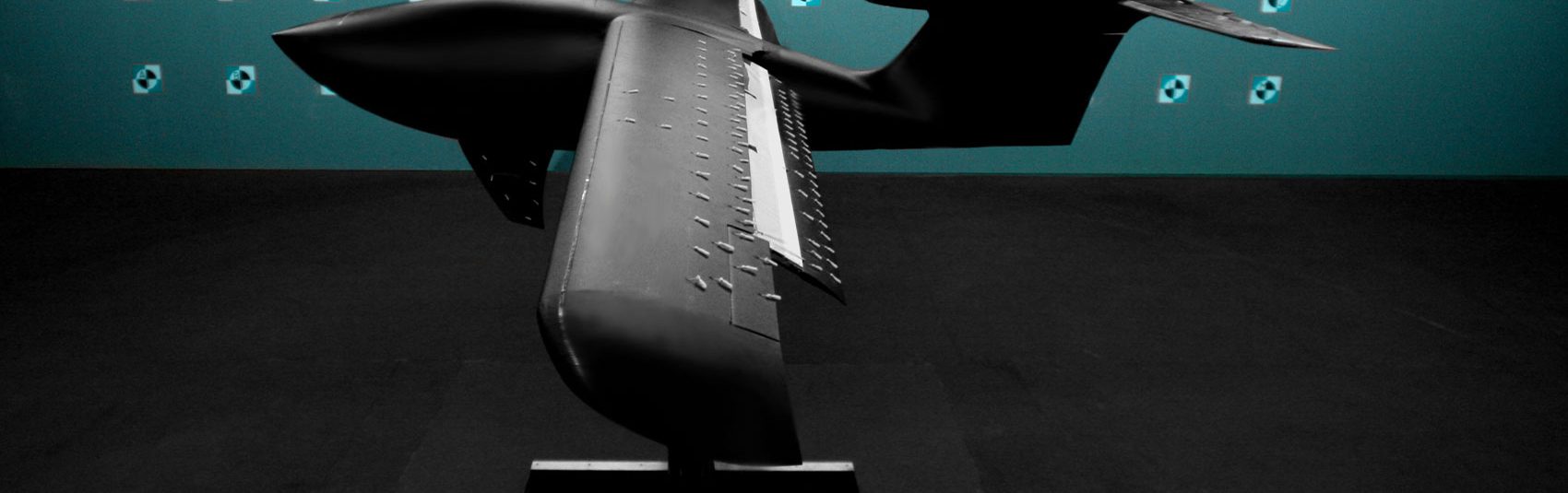
From the model to the prototype
Once the optimal configuration had been defined, the technical office created a 1:1 scale prototype. Using composite materials require true expertise with regard to the structural design and manufacturing of the parts.
In this part of the design process, LISA’s engineers relied on their extensive experience of analysing composite parts. Among the various stages in the analysis process, the finite element analysis (FEA) makes it possible to obtain a greater level of detail with regard to the composition of a part, visualize the deformation under load, and verify that sufficient margins of safety exist for the entire flight envelope.
Lastly, all the parts of the AKOYA’s primary structure were stressed to breaking point during static load testing in order to verify that their manufacture was consistent with the calculations, and that each part had optimal weight and resistance.
The flight test program made it possible to finalize the development phase, explore the flight envelope, and acquire all the data necessary for the aircraft’s certification by the authorities.