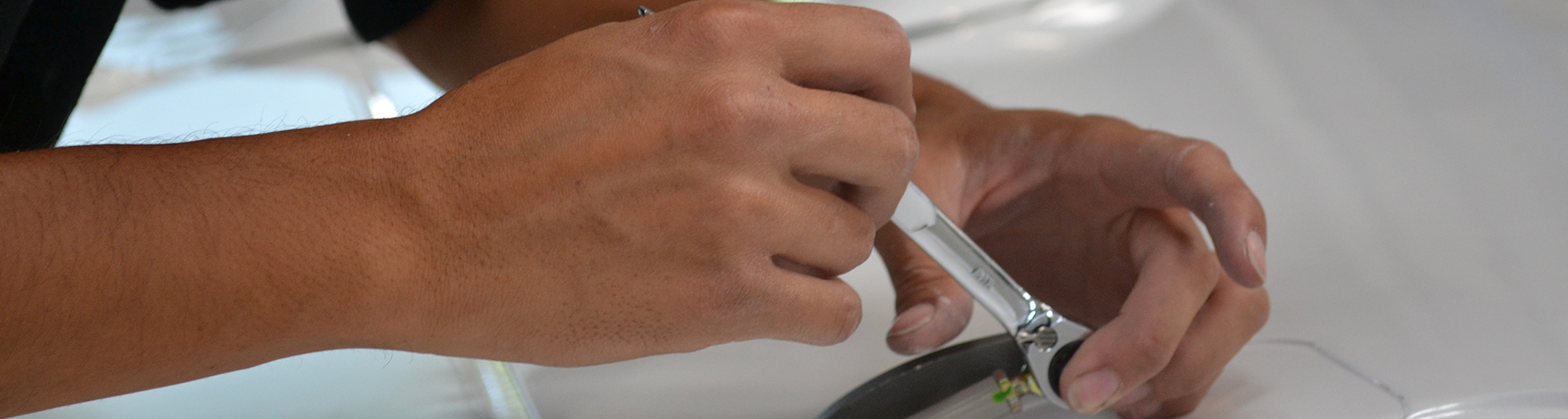
Producing an aircraft fitted with so much equipment with an overall unladen weight of 882 lbs is quite a challenge. To achieve this incredibly ambitious goal, LISA’s engineers, who are experts in the use of composite materials, have excelled at using these materials and succeeded in optimizing the AKOYA’s overall weight, while maintaining a high degree of strength and a remarkable surface finish. In view of its functionality and the quality of its equipment and finish, the AKOYA is undoubtedly the lightest aircraft on the market.
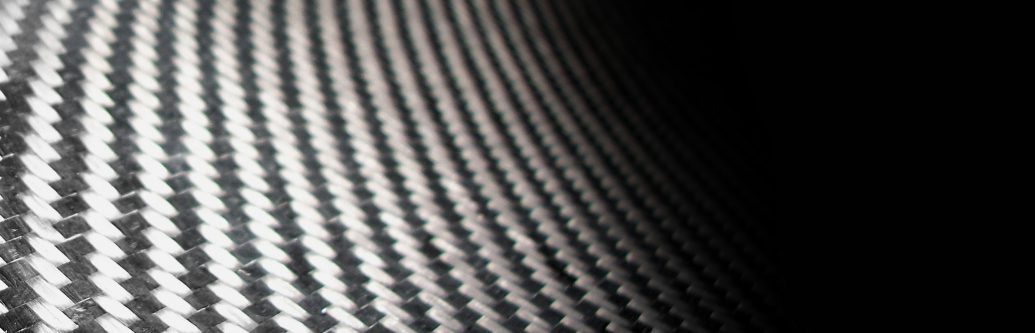
The fuselage, airfoils, and most of the components are made from an ingenious combination of fiberglass, Kevlar, high-density hydrophobic foam, and, above all, high-quality carbon fiber pre-impregnated with epoxy resin. This carbon material, which is used in boat and motor racing, is known for its rigidity, exceptional durability, and a very high strength-to-weight ratio. Only the moveable mechanical parts, such as the landing gear and the wing pivot systems, are made from titanium and aluminum. All these components are protected against corrosion so that they can be used in a marine environment.
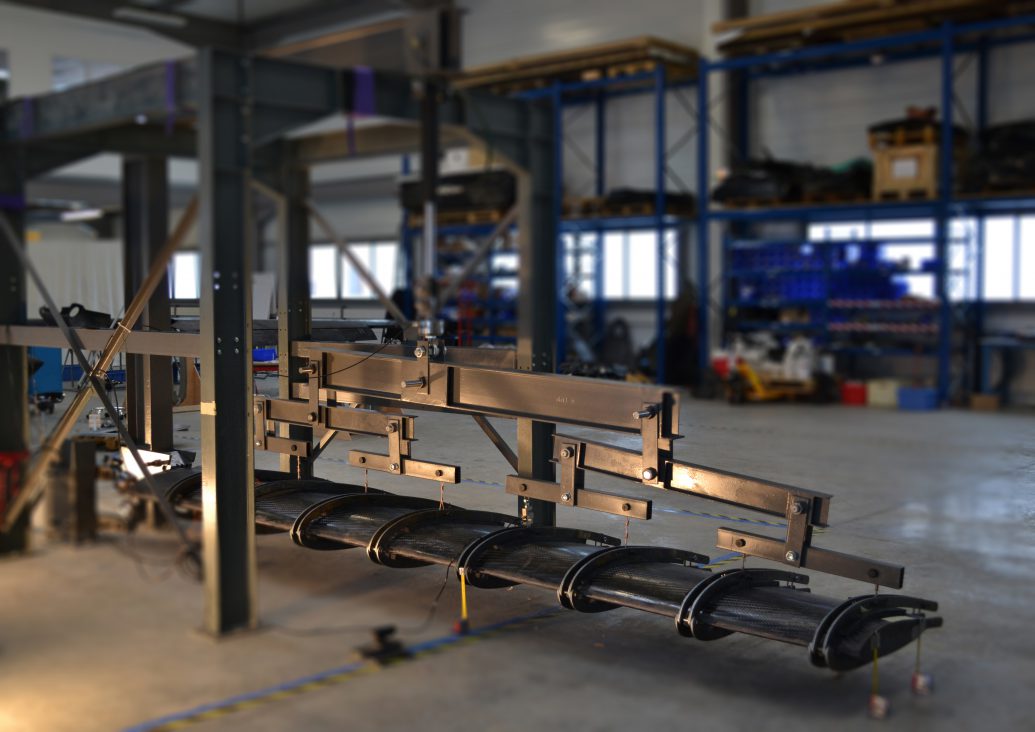
An advanced and rigorous manufacturing process
LISA has developed a meticulous industrial process, enabling the company to produce its airplanes according to extremely strict specifications, and ensure optimal quality control at every stage of the manufacturing process. The company’s decision to use composite materials as the main material for the construction of its airplanes sets the bar even higher, as the manufacturing method requires a workforce with very specific skills and rigorous expertise. Each stage of the production process requires specific skills to ensure the right combination and balance of the materials.
Hence, the various subcontractors are chosen in a very methodical way according to strict criteria and very high standards in terms of expertise, know-how, means of production, organizational capacity, and medium-term viability, in order to ensure the production of the 225 molds and 2,500 components of which each aircraft is comprised.
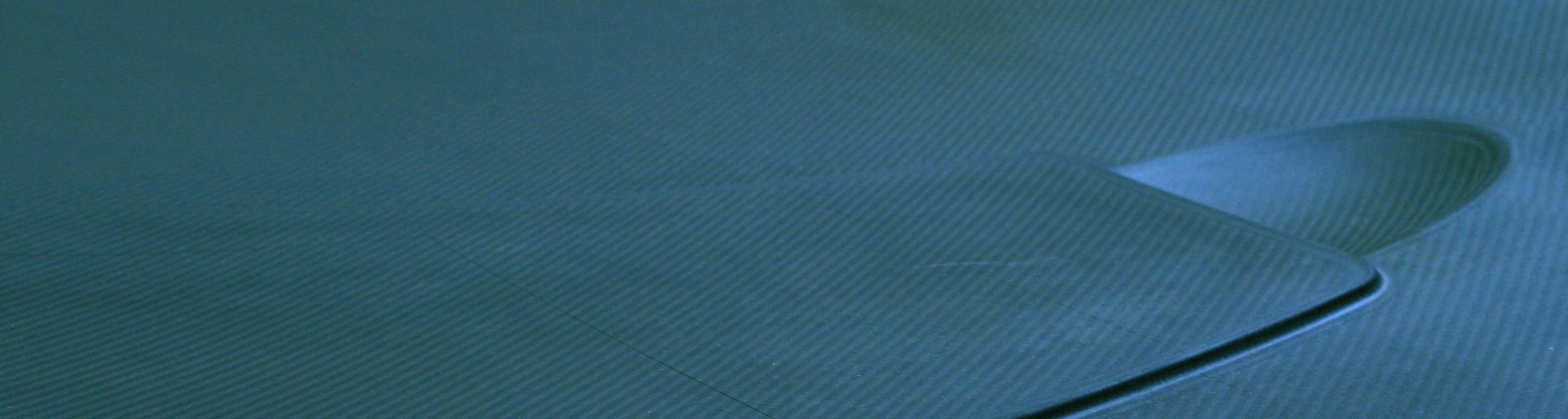
Made in France & Europe
The AKOYA has been entirely conceived and designed in our offices, in the heart of the French Alps. This is also where we carry out all the tests and the final assembly of our airplanes.
The expertise of French companies in the aviation sector contributes to the manufacture of most of the composite components, mechanical elements, and flight controls; the remainder of the work is entrusted to partners in neighboring countries (Italy, Germany, and Switzerland).
In addition to the rigor, precision, and quality of finish provided by these subcontractors, the geographical proximity makes it possible to carry out regular checks and ensures a high level of reactivity with optimal results.