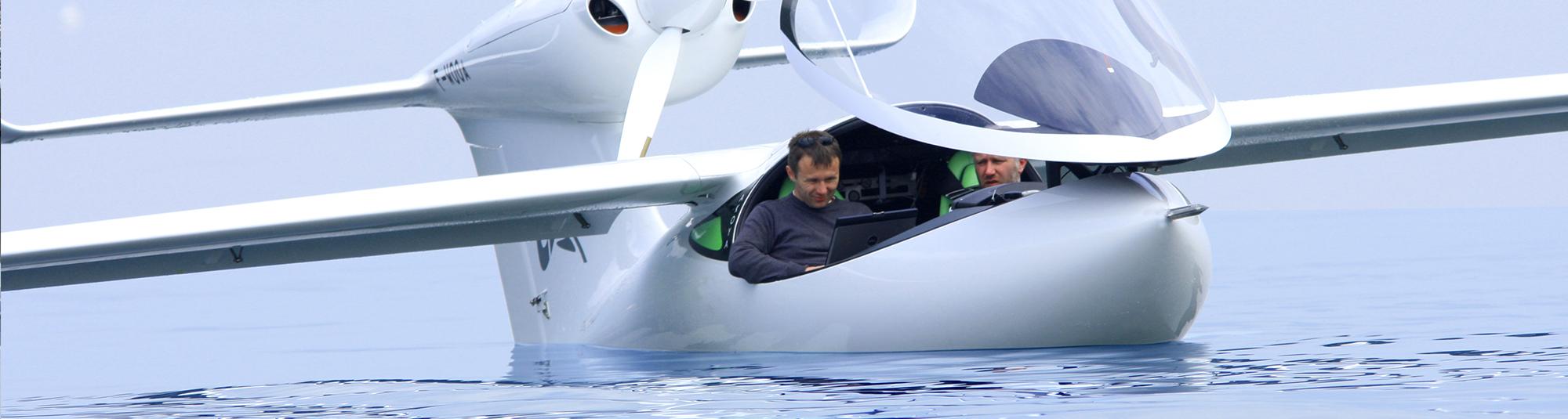
Pour créer une nouvelle génération d’avions, il ne s’agissait évidemment pas de réinterpréter une conception d’avion existante. Nous devions réellement partir d’une feuille blanche, en mettant de côté toutes les idées reçues, pour démarrer avec un regard neuf et proposer des solutions radicalement différentes de l’existant.
Mélange de matière grise, d’inventivité et de rigueur
Rêves et vision ambitieuse de l’aviation sont toujours les points de départ de nos travaux R&D. Aérodynamique, hydrodynamique, mécanique, science des matériaux et électrotechnique : armés de ces compétences les ingénieurs de très haut niveau de LISA font preuve d’inventivité, d’exigence et de rigueur. Toute l’équipe prend alors plaisir à relever les défis pour proposer des solutions inédites face à ces « missions impossibles » exigées par notre vision.
Une fois les innovations protégées par des brevets internationaux, la démarche scientifique rigoureuse de nos ingénieurs peut commencer : Calculs analytiques, calculs par éléments finis, essais par similitude sur maquettes, essais en vol, … Toutes ces étapes sont rebouclées jusqu’à aboutir à une solution industrialisable. Et au-delà de l’application, nos ingénieurs R&D ont pour mission de constituer un véritable savoir-faire exploitable sur d’autres avions.
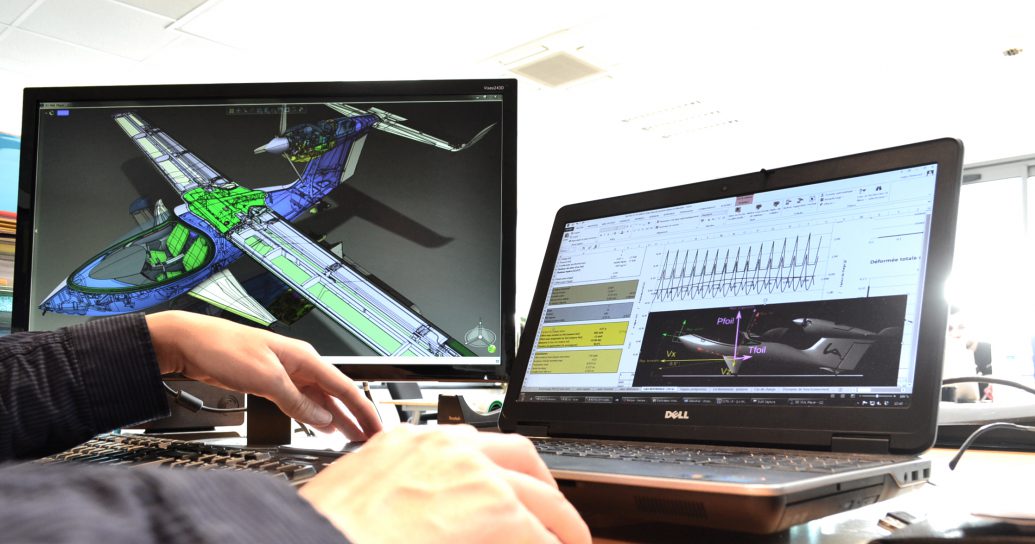
Un processus créatif rodé
Rendre concrètes les multiples idées ingénieuses qui constituent nos avions a demandé un travail intense de la part des ingénieurs et des années de recherche et développement. Des études poussées combinant les contraintes aérodynamiques et nautiques ont été menées pour matérialiser chacun des concepts, puis mettre en musique l’ensemble, afin d’obtenir une configuration optimale.
Une fois validée par les calculs et essais en simulation numérique, chaque configuration est ensuite testée sur des maquettes à l’échelle 1/3. Des essais en soufflerie à l’ONERA (centre français de recherche aérospatiale) ont permis d’optimiser les surfaces aérodynamiques, ceux en bassins de carène ont confirmé les atouts des Seafoils, tandis que les essais sur maquettes radiocommandées en milieu naturel ont permis de valider les grandes caractéristiques de vol et la maniabilité de l’avion sur chaque terrain.
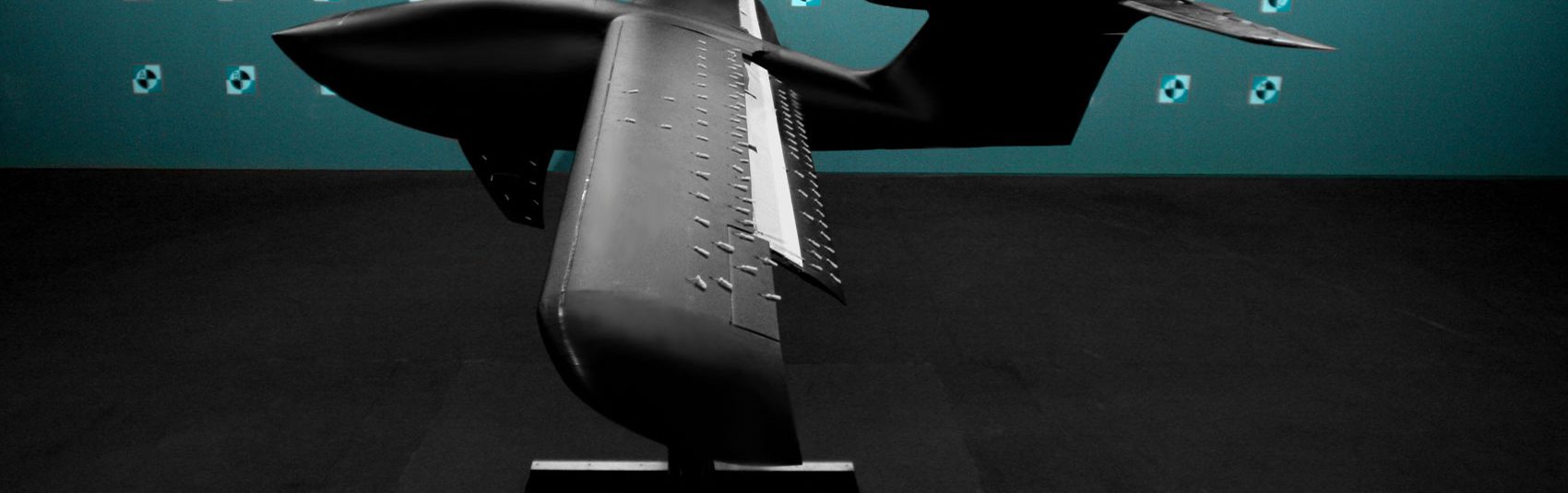
De la maquette au prototype
Une fois la configuration optimale définie, le bureau d’études entre en jeu pour réaliser le prototype échelle 1. Les avantages indéniables que présentent l’utilisation de matériaux composite nécessitent néanmoins une réelle expertise dans le dimensionnement structurel et la fabrication des pièces.
Pour cette partie, les ingénieurs LISA se sont appuyés sur une solide expérience de calcul de pièces composite. Parmi les différentes étapes de calcul, la méthode des éléments finis permet d’obtenir un niveau de détail supplémentaire concernant la composition d’une pièce, de visualiser les déformations auxquelles elle est soumise et de vérifier que le facteur de sécurité est respecté dans l’ensemble du domaine de vol de l’appareil.
Enfin, toutes les pièces de la structure primaire de l’AKOYA ont été testées par essais statiques jusqu’à leur point de rupture afin de vérifier que la fabrication était conforme aux calculs et que la masse et la résistance de chaque pièce étaient optimales.
La campagne d’essais en vol permet, quant à elle de finaliser la mise au point, d’ouvrir le domaine de vol de l’avion et de capitaliser l’ensemble des données nécessaires à la certification de l’appareil par les autorités.